12 Expert Tips For Proven Process Capability Index Calculation Success Quickly

The Process Capability Index (Cp, Cpk) is a statistical measure used to determine the ability of a process to produce output within specified limits. Calculating the Process Capability Index is crucial in understanding the performance of a process and identifying areas for improvement. In this article, we will provide 12 expert tips for proven Process Capability Index calculation success, helping you to quickly and accurately determine the capability of your processes.
Understanding the Basics of Process Capability Index
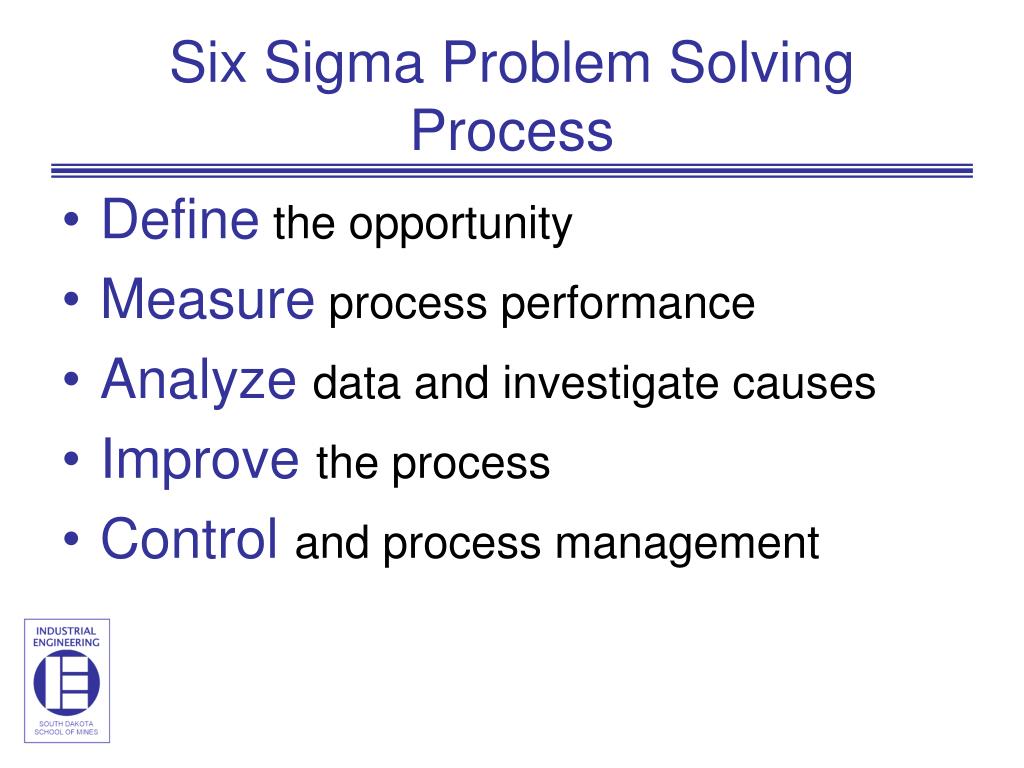
Before diving into the tips, it’s essential to understand the basics of the Process Capability Index. The Process Capability Index is calculated using the following formula: Cp = (USL - LSL) / 6σ, where USL is the upper specification limit, LSL is the lower specification limit, and σ is the standard deviation of the process. The Cpk is a modified version of the Cp, which takes into account the mean of the process: Cpk = min(USL - μ, μ - LSL) / 3σ, where μ is the mean of the process. Understanding these formulas is crucial for accurate calculation of the Process Capability Index.
Tip 1: Define Specification Limits
Defining the specification limits is the first step in calculating the Process Capability Index. Specification limits are the upper and lower limits within which the process output should fall. It’s essential to define these limits clearly and accurately, as they will be used to calculate the Process Capability Index. Ensure that the specification limits are realistic and achievable, taking into account the capabilities of the process and the requirements of the customer.
Tip 2: Collect Relevant Data
Collecting relevant data is critical in calculating the Process Capability Index. The data should be representative of the process and should include a sufficient number of samples to ensure accuracy. The data should also be collected over a reasonable period, taking into account any changes in the process that may affect the output.
Tip 3: Calculate the Mean and Standard Deviation
Calculating the mean and standard deviation of the process is essential in determining the Process Capability Index. The mean is the average value of the process output, while the standard deviation is a measure of the variability of the process. Standard deviation is calculated using the formula: σ = √(Σ(xi - μ)^2 / (n - 1)), where xi is the individual data point, μ is the mean, and n is the number of samples.
Statistical Measure | Formula |
---|---|
Mean | μ = Σxi / n |
Standard Deviation | σ = √(Σ(xi - μ)^2 / (n - 1)) |

Tip 4: Determine the Cp and Cpk
Using the formulas mentioned earlier, determine the Cp and Cpk values. The Cp value will provide an indication of the potential capability of the process, while the Cpk value will provide an indication of the actual capability of the process, taking into account the mean of the process.
Tip 5: Interpret the Results
Interpreting the results of the Process Capability Index calculation is crucial in understanding the performance of the process. A Cp value of 1.33 or higher indicates that the process is capable of producing output within the specified limits, while a Cpk value of 1.33 or higher indicates that the process is not only capable but also centered around the target value.
Tip 6: Identify Areas for Improvement
Identifying areas for improvement is essential in optimizing the process. Analyze the data to determine the causes of any variability or deviations from the target value. Root cause analysis techniques can be used to identify the underlying causes of the problems and develop strategies for improvement.
Tip 7: Implement Corrective Actions
Implementing corrective actions is critical in optimizing the process. Develop a plan to address the areas for improvement identified in the previous step. The plan should include specific actions, responsibilities, and timelines for implementation.
Tip 8: Monitor and Control the Process
Monitoring and controlling the process is essential in ensuring that the improvements are sustained over time. Establish a system for monitoring the process and tracking key performance indicators. Statistical process control techniques can be used to monitor the process and detect any deviations from the target value.
Tip 9: Continuously Improve the Process
Continuously improving the process is critical in achieving long-term success. Encourage a culture of continuous improvement within the organization, where employees are empowered to identify areas for improvement and develop strategies for implementation.
Tip 10: Use Software Tools
Using software tools can simplify the Process Capability Index calculation and improve accuracy. Choose a software tool that is user-friendly and provides the necessary functionality for calculating the Process Capability Index.
Tip 11: Document the Results
Documenting the results of the Process Capability Index calculation is essential in maintaining a record of the process performance. Keep a record of the data collected, calculations performed, and results obtained. This will help in tracking progress over time and identifying areas for improvement.
Tip 12: Provide Training and Support
Providing training and support is critical in ensuring that employees understand the Process Capability Index calculation and can apply it effectively. Provide training on the concepts and techniques involved in calculating the Process Capability Index, and offer support to employees as needed.
What is the difference between Cp and Cpk?
+Cp is a measure of the potential capability of the process, while Cpk is a measure of the actual capability of the process, taking into account the mean of the process. A process with a high Cp value but a low Cpk value may be capable of producing output within the specified limits, but may not be centered around the target value.
How do I interpret the results of the Process Capability Index calculation?
+A Cp value of 1.33 or higher indicates that the process is capable of producing output within the specified limits, while a Cpk value of 1.33 or higher indicates that the process is not only capable but also centered around the target value. A low Cp or Cpk value indicates that the process may not be capable of producing output within the specified limits, and improvements may be necessary.
In conclusion, calculating the Process Capability Index is a critical step in understanding the performance of a process and identifying areas for improvement. By following the 12 expert tips outlined in this article, you can quickly and accurately determine the capability of your processes and make informed decisions about process improvement. Remember to continuously monitor and control the process, and continuously improve the process to achieve long-term success.