How To Calculate Capability Index For Reliable Manufacturing Process Optimization Quickly

The capability index is a statistical measure used to evaluate the ability of a manufacturing process to produce output within specified limits. It is a crucial metric for process optimization, as it helps manufacturers identify areas for improvement and ensure that their processes are reliable and efficient. In this article, we will discuss how to calculate the capability index for a reliable manufacturing process optimization quickly.
Understanding Capability Index
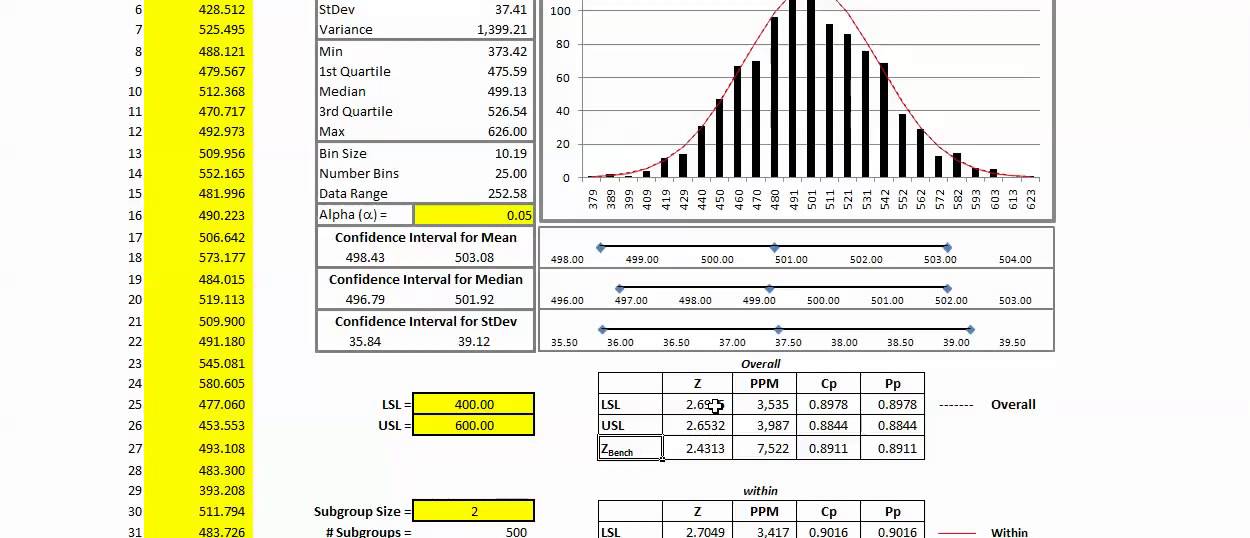
The capability index is a dimensionless value that compares the width of the specification limits to the width of the process distribution. It is typically denoted by the symbols Cp, Cpk, or Pp, depending on the type of calculation used. The most common types of capability indices are:
- Cp (Capability Index): This index measures the spread of the process data relative to the specification limits.
- Cpk (Centered Capability Index): This index measures the spread of the process data relative to the specification limits, taking into account the centering of the process.
- Pp (Performance Index): This index measures the spread of the process data relative to the specification limits, based on the performance of the process.
Each of these indices provides valuable insights into the process capability and can be used to identify areas for improvement.
Calculating Capability Index
To calculate the capability index, you need to follow these steps:
- Collect data: Collect a sample of data from the process, including the specification limits.
- Calculate the mean: Calculate the mean of the process data.
- Calculate the standard deviation: Calculate the standard deviation of the process data.
- Calculate the Cp: Use the formula Cp = (USL - LSL) / (6 * σ), where USL is the upper specification limit, LSL is the lower specification limit, and σ is the standard deviation.
- Calculate the Cpk: Use the formula Cpk = min[(USL - μ) / (3 * σ), (μ - LSL) / (3 * σ)], where μ is the mean.
- Calculate the Pp: Use the formula Pp = (USL - LSL) / (6 * σ), where σ is the standard deviation of the performance data.
These calculations can be performed using statistical software or spreadsheet programs.
Capability Index | Formula | Description |
---|---|---|
Cp | (USL - LSL) / (6 * σ) | Measures the spread of the process data relative to the specification limits. |
Cpk | min[(USL - μ) / (3 * σ), (μ - LSL) / (3 * σ)] | Measures the spread of the process data relative to the specification limits, taking into account the centering of the process. |
Pp | (USL - LSL) / (6 * σ) | Measures the spread of the process data relative to the specification limits, based on the performance of the process. |

Interpreting Capability Index Results
The capability index results can be interpreted as follows:
- Cp ≥ 1.33: The process is capable of producing output within the specification limits.
- 1.00 ≤ Cp < 1.33: The process is marginally capable of producing output within the specification limits.
- Cp < 1.00: The process is not capable of producing output within the specification limits.
- Cpk ≥ 1.33: The process is centered and capable of producing output within the specification limits.
- 1.00 ≤ Cpk < 1.33: The process is marginally centered and capable of producing output within the specification limits.
- Cpk < 1.00: The process is not centered and not capable of producing output within the specification limits.
These interpretations can help manufacturers identify areas for improvement and optimize their processes for better performance.
What is the difference between Cp and Cpk?
+Cp measures the spread of the process data relative to the specification limits, while Cpk takes into account the centering of the process. Cpk is a more comprehensive measure of process capability, as it considers both the spread and the centering of the process.
How do I calculate the standard deviation of the process data?
+The standard deviation of the process data can be calculated using the formula σ = √[(Σ(x - μ)^2) / (n - 1)], where x is the individual data point, μ is the mean, and n is the sample size. This calculation can be performed using statistical software or spreadsheet programs.
In conclusion, calculating the capability index is a crucial step in optimizing manufacturing processes for reliability and efficiency. By following the steps outlined in this article, manufacturers can quickly and accurately calculate the capability index and identify areas for improvement. Remember to interpret the results correctly, taking into account the type of capability index used and the specification limits. With the right approach, manufacturers can ensure that their processes are capable of producing high-quality output and meet customer requirements.