When To Use 5S Six Sigma Tools For Root Cause Analysis And Problemsolving?

The 5S methodology, originating from Japan, is a systematic approach to workplace organization and standardization. It consists of five phases: Sort, Set in Order, Shine, Standardize, and Sustain. Six Sigma, on the other hand, is a data-driven approach to quality management that aims to reduce defects and variations in processes. When combined, 5S and Six Sigma tools can be powerful methods for root cause analysis and problem-solving. In this context, we will explore when to use these tools to achieve effective problem-solving and process improvement.
Introduction to 5S and Six Sigma
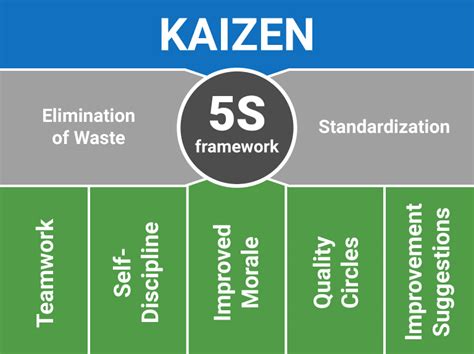
The 5S methodology is designed to create a well-organized and efficient work environment. It involves sorting and removing unnecessary items, setting in order the necessary items, shining and cleaning the workplace, standardizing work processes, and sustaining the new order. Six Sigma, with its DMAIC (Define, Measure, Analyze, Improve, Control) framework, provides a structured approach to problem-solving and process improvement. By integrating 5S with Six Sigma, organizations can enhance their problem-solving capabilities and achieve significant improvements in quality and efficiency.
Root Cause Analysis with 5S and Six Sigma
Root cause analysis is a critical step in problem-solving, as it helps identify the underlying causes of problems rather than just treating their symptoms. The 5S methodology can be used to prepare the environment for root cause analysis by removing clutter, organizing workflows, and standardizing processes. Six Sigma tools, such as the Fishbone diagram (Ishikawa diagram) and the 5 Whys method, can then be applied to drill down to the root cause of the problem. The Fishbone diagram is particularly useful for identifying potential causes and categorizing them into different groups, such as equipment, materials, and processes. The 5 Whys method involves asking “why” five times to drill down to the root cause of the problem.
5S Phase | Six Sigma Tool | Purpose |
---|---|---|
Sort | Fishbone diagram | Identify potential causes of problems |
Set in Order | 5 Whys method | Drill down to the root cause of problems |
Shine | Pareto analysis | Identify the most significant problems |
Standardize | Control charts | Monitor and control processes |
Sustain | Lessons learned document | Document and share knowledge |

When to Use 5S and Six Sigma Tools
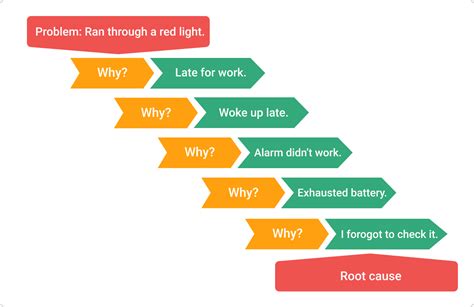
5S and Six Sigma tools can be used in various situations, including:
- Process improvements: When processes are inefficient, wasteful, or prone to errors, 5S and Six Sigma tools can help identify areas for improvement and implement changes.
- Problem-solving: When problems arise, 5S and Six Sigma tools can help identify the root cause and implement effective solutions.
- Quality management: When quality issues arise, 5S and Six Sigma tools can help identify the causes and implement corrective actions.
- Change management: When changes are implemented, 5S and Six Sigma tools can help ensure a smooth transition and minimize disruptions.
Benefits of Using 5S and Six Sigma Tools
The benefits of using 5S and Six Sigma tools include:
- Improved efficiency: By streamlining processes and eliminating waste, organizations can improve productivity and efficiency.
- Enhanced quality: By identifying and addressing quality issues, organizations can improve customer satisfaction and loyalty.
- Increased employee engagement: By involving employees in the problem-solving process, organizations can improve morale and motivation.
- Reduced costs: By eliminating waste and improving processes, organizations can reduce costs and improve profitability.
What is the primary purpose of the 5S methodology?
+The primary purpose of the 5S methodology is to create a well-organized and efficient work environment by sorting, setting in order, shining, standardizing, and sustaining the workplace.
How does Six Sigma support root cause analysis?
+Six Sigma supports root cause analysis through the use of tools such as the Fishbone diagram and the 5 Whys method, which help identify the underlying causes of problems.
What are the benefits of combining 5S and Six Sigma tools?
+The benefits of combining 5S and Six Sigma tools include improved efficiency, enhanced quality, increased employee engagement, and reduced costs.